The difference and comparison of laser cutting, water cutting, plasma cutting, and wire cutting
Laser cutting samples
Listen to an engineer in the cutting field say:
1) At present, the mainstream fiber lasers in the market, carbon dioxide lasers are gradually eliminated, and the energy consumption is too high. There is still a market in the non-metallic field.
2) The price of fiber optic equipment has dropped drastically in the low and medium power range since the laser was made in China.
3) In addition to laser cutting methods, the market demand for plasma and wire cutting is relatively large, but wire cutting is targeted at more mold industries. Plasma is in demand for thick plates or low precision requirements. Waterjet cutting is now It is no longer common in the metal industry, and there are many in the non-metal field.
4) In the future development, laser cutting is absolutely the world of thin metal plates, including non-metal cutting, laser cutting will occupy a considerable part of the market.
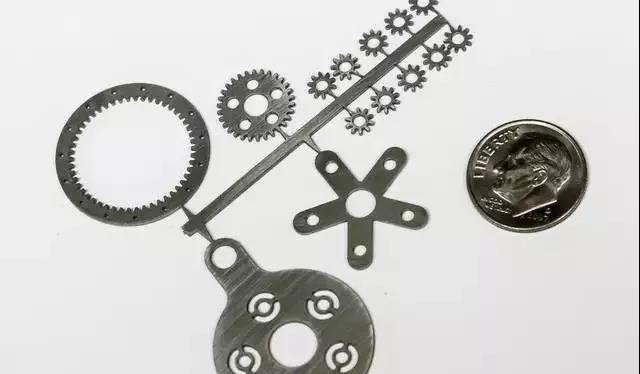
Water cutting samples
If you have any different opinions, you can speak freely in the message area. Next, let's analyze these cutting technologies.
Laser cutting processing
Optical cutting is the use of a focused high-power density laser beam to irradiate the workpiece to quickly melt, vaporize, ablate or reach the ignition point of the irradiated material. At the same time, the molten material is blown away by the high-speed airflow coaxial with the beam to realize the cutting of the workpiece. open. Currently, CO2 pulsed lasers are generally used, and laser cutting is one of the thermal cutting methods.
A recently popular laser cutting video
Water cutting
Water cutting, also known as water jet, is a high-pressure water jet cutting technology, which is a machine that uses high-pressure water to cut. Under the control of the computer, the workpiece can be carved at will, and it is not affected by the texture of the material. Water cutting is divided into two methods: no sand cutting and sand cutting.
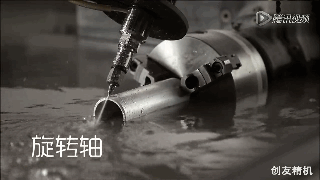
Plasma cutting
Plasma arc cutting is a processing method that uses the heat of a high-temperature plasma arc to locally melt (and evaporate) the metal at the incision of the workpiece, and use the momentum of the high-speed plasma to remove the molten metal to form an incision.
Plasma cutting steel pipe video from Japan
Wire cutting
Wire Electrical Discharge Machining (WEDM for short) belongs to the category of electrical machining. Wire cut Electrical Discharge Machining (WEDM for short) is sometimes also called WEDM. Wire cutting can be divided into fast wire cutting, medium wire cutting, and slow wire cutting. The wire speed of fast wire EDM wire cutting is 6-12 m/s, and the electrode wire moves back and forth at high speed, so the cutting accuracy is poor. Medium wire EDM is a new technology developed in recent years to realize the function of frequency conversion multiple cutting on the basis of fast wire wire cutting. The wire speed of slow wire EDM wire cutting is 0.2m/s, and the electrode wire moves in one direction at a low speed, so the cutting accuracy is very high.
Slow wire cutting video
Application range comparison
The laser cutting machine has a wide range of applications. Regardless of metal or non-metal, it can cut and cut non-metal, such as cloth, leather, etc. with CO2 laser cutting machine, and for cutting metal with fiber laser cutting machine. The plate deformation is small.
Water cutting is cold cutting, no thermal deformation, good cutting surface quality, no secondary processing, and easy secondary processing if necessary. Water cutting can perforate and cut any material, with fast cutting speed and flexible processing size.
Plasma cutting machine can be used for cutting various metal materials such as stainless steel, aluminum, copper, cast iron, carbon steel, etc. Plasma cutting has obvious thermal effect, low precision, and it is not easy to perform secondary processing on the cut surface.
Wire cutting can only cut conductive materials, and cutting coolant is required during the cutting process, so materials that are not conductive, afraid of water, and afraid of contamination by cutting coolant, such as paper and leather, cannot be cut.
Cutting thickness comparison
The industrial application of laser cutting carbon steel is generally below 20mm. The cutting capacity is generally below 40mm. Stainless steel industrial applications are generally below 16mm, and the cutting capacity is generally below 25mm. And as the thickness of the workpiece increases, the cutting speed decreases significantly.
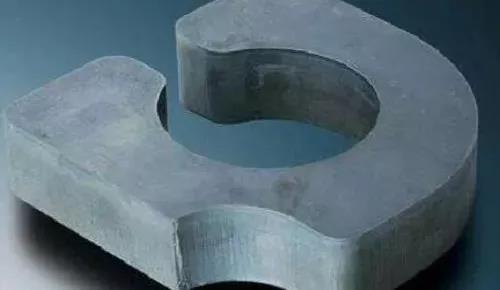
Breakthrough 30mm fiber laser cutting sheet
The thickness of water cutting can be very thick, 0.8-100mm, or even thicker materials.
The plasma cutting thickness is 0-120mm, and the best cutting quality range is about 20mm. The plasma system has the highest cost performance.
The thickness of wire cutting is generally 40-60mm, and the maximum thickness can reach 600mm.
Cutting speed comparison
Using a laser with a power of 1200W to cut 2mm thick low-carbon steel plates, the cutting speed can reach 600cm/min; for 5mm thick polypropylene resin plates, the cutting speed can reach 1200cm/min. The cutting efficiency that can be achieved by wire EDM is generally 20-60 square millimeters/minute, and the highest can reach 300 square millimeters/minute; obviously, the laser cutting speed is fast and can be used for mass production.
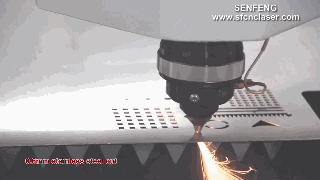
The water cutting speed is quite slow and not suitable for mass production.
The cutting speed of plasma cutting is slow and the relative accuracy is low. It is more suitable for cutting thick plates, but the end surface has a slope.
For metal processing, wire cutting has higher precision, but the speed is very slow. Sometimes other methods are needed to punch and thread to cut, and the cutting size is greatly limited.
Cutting accuracy comparison
The laser cutting incision is narrow, the two sides of the incision seam are parallel and perpendicular to the surface, and the dimensional accuracy of the cut parts can reach ±0.2mm.
The plasma can reach within 1mm.
Water cutting will not produce thermal deformation, and the accuracy is ±0.1mm. If a dynamic waterjet machine is used, the cutting accuracy can be improved, and the cutting accuracy can reach ±0.02mm, eliminating the cutting slope.
The machining accuracy of wire cutting is generally ±0.01~±0.02mm, up to ±0.004mm.
Comparison of slit width
Laser cutting is more precise than plasma cutting, and the cutting gap is small, about 0.5mm.
The slit of plasma cutting is larger than laser cutting, about 1-2mm.
The cutting seam of water cutting is about 10% larger than the diameter of the knife tube, generally 0.8-1.2mm. As the diameter of the sand knife tube expands, the incision becomes larger.
The width of the slit for wire cutting is the smallest, generally about 0.1-0.2mm.
Cut surface quality comparison
The surface roughness of laser cutting is not as good as water cutting, the thicker the material, the more obvious.
Water cutting will not change the texture of the material around the cutting seam (laser is a thermal cutting and will change the texture of the cutting area).
Production input cost comparison
1) Different models of laser cutting machines have different prices. Cheap ones such as carbon dioxide laser cutting machines only cost 20,000 to 30,000, and expensive ones such as 1000W fiber laser cutting machines now cost more than one million. Laser cutting has no consumables, but the equipment investment cost is the highest among all cutting methods, and it is not a little bit higher, and the use and maintenance costs are also quite high.
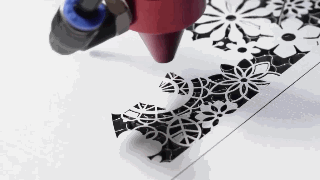
2) Plasma cutting machine is much cheaper than laser cutting machine. According to the power and brand of plasma cutting machine, the price is different and the use cost is higher. Basically, as long as it can cut conductive materials.
3) The cost of water cutting equipment is second only to laser cutting, with high energy consumption and high maintenance costs. The cutting speed is not as fast as plasma, because all abrasives are disposable, and they are discharged into the nature once used. , So the environmental pollution caused is also more serious.
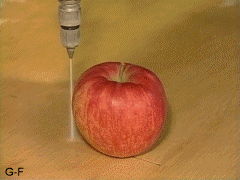
4) Wire cutting is generally around tens of thousands of yuan. However, there are consumables for wire cutting, such as molybdenum wire and cutting coolant. There are two kinds of wire commonly used in wire cutting. One is molybdenum wire (molybdenum is precious), which is used in fast-moving wire equipment. The advantage is that molybdenum wire can be reused many times; the other is copper wire (which is much cheaper than molybdenum wire anyway).了), used for slow wire walking equipment, the disadvantage is that the copper wire can only be used once. In addition, the fast-moving wire machine is far cheaper than the slow-moving wire machine. The price of a slow-moving wire is equal to 5 or 6 fast-moving wires.
Latest News
Contact Us
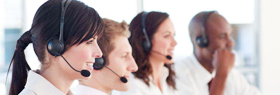
Name: Kevin Hu
Tel: +86-18026978395
E-mail: [email protected]
Skype: recometaltech
WeChat: RECOMETALTECH
Whatsapp: +86 180 2697 8395
Add: Datianyang Industrial Zone,Songgang Street, Baoan District, Shenzhen,China.